Ok I am stuck. I need some help from someone who has experience making gun springs. But not just gun springs, very SMALL / THIN springs.
To get it out of the way up front. I have successfully made obsolete gun springs before. This is a very old gun (Hood International No. 3, .32rf). No replacement springs are available for it anywhere, trust me I have looked. I am starting with flat tempered spring material purchased at this thickness.
I believe my issues revolve around holding such a very small spring while trying to go through the production steps after grinding/filing to size:
1) Heating and bending to dimensions (MAAP Torch)
2) Heating and quenching (MAAP Torch + Brownell's Quenching Oil)
3) Tempering (Lead milting pot)
While I understand that I do not know everything about spring making, I believe my issues surround the extremely small size of the spring. This is more like a watch spring than a gun spring in size. My results after several attempts are springs that snap upon use or when testing before use. I believe because the size is so small, that I am not getting even heating of the metal. On this small spring I have trouble with:
< Not able to bend the metal into a shape quick enough before the item has cooled (Causing Stress)
< Not evenly heating the spring to cherry red prior to quenching (Portion I am holding does not get cherry?)
< Possibly not heating the spring evenly during tempering (Have to hold it somewhere, right?)
I understand all these thing are basic, but I need some ideas on how to accomplish this on a spring so small that holding it anywhere causes that surrounding area of the spring not to heat sufficiently. This seems to result in stress in the metal causing breakage in usage after a few cycles, or even before it passes initial test bending.
To understand the small size, here are the finished spring dimensions:
.017" = Spring Thickness
.070" = Spring width
I have also attached a diagram of the spring in its 3 positions: Static, minimum installed compression, & fully compressed.
Thanks for any suggestions,
Bruce
To get it out of the way up front. I have successfully made obsolete gun springs before. This is a very old gun (Hood International No. 3, .32rf). No replacement springs are available for it anywhere, trust me I have looked. I am starting with flat tempered spring material purchased at this thickness.
I believe my issues revolve around holding such a very small spring while trying to go through the production steps after grinding/filing to size:
1) Heating and bending to dimensions (MAAP Torch)
2) Heating and quenching (MAAP Torch + Brownell's Quenching Oil)
3) Tempering (Lead milting pot)
While I understand that I do not know everything about spring making, I believe my issues surround the extremely small size of the spring. This is more like a watch spring than a gun spring in size. My results after several attempts are springs that snap upon use or when testing before use. I believe because the size is so small, that I am not getting even heating of the metal. On this small spring I have trouble with:
< Not able to bend the metal into a shape quick enough before the item has cooled (Causing Stress)
< Not evenly heating the spring to cherry red prior to quenching (Portion I am holding does not get cherry?)
< Possibly not heating the spring evenly during tempering (Have to hold it somewhere, right?)
I understand all these thing are basic, but I need some ideas on how to accomplish this on a spring so small that holding it anywhere causes that surrounding area of the spring not to heat sufficiently. This seems to result in stress in the metal causing breakage in usage after a few cycles, or even before it passes initial test bending.
To understand the small size, here are the finished spring dimensions:
.017" = Spring Thickness
.070" = Spring width
I have also attached a diagram of the spring in its 3 positions: Static, minimum installed compression, & fully compressed.
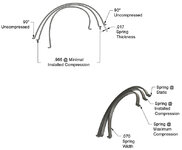
Thanks for any suggestions,
Bruce