My Redding full length sizing die is resulting in the case headspace below SAAMI spec as low as 1.453".
(SAAMI spec is 1.4666 max to 1.4596 min)
I did not notice this when I started working on a load for 223 because I knew I wanted to FL size for a semi auto and not bother with shoulder bumping, I assumed a full length sizing die would not be made to produce out of spec brass. Only out of curiosity I checked some samples and found this....
I did a ladder test found a charge and reloaded another batch and confirmed the recipe. Today I wanted to load some rounds to that recipe using some resized cases and some new virgin brass... the virgin brass is in spec, I was going to resize them anyways to make everything consistent and the same so I checked them and found the difference so I checked the saami spec.
So now Im wondering what to do? Is it bad to run out of tolerance on the small end? Or should I start over and start backing off the FL die to get the correct case headspace?
(SAAMI spec is 1.4666 max to 1.4596 min)
I did not notice this when I started working on a load for 223 because I knew I wanted to FL size for a semi auto and not bother with shoulder bumping, I assumed a full length sizing die would not be made to produce out of spec brass. Only out of curiosity I checked some samples and found this....
I did a ladder test found a charge and reloaded another batch and confirmed the recipe. Today I wanted to load some rounds to that recipe using some resized cases and some new virgin brass... the virgin brass is in spec, I was going to resize them anyways to make everything consistent and the same so I checked them and found the difference so I checked the saami spec.
So now Im wondering what to do? Is it bad to run out of tolerance on the small end? Or should I start over and start backing off the FL die to get the correct case headspace?
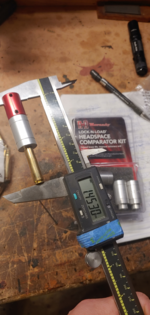