Member 5605
- Messages
- 11,671
- Reactions
- 23,702
I know NOTHING but what I have read. I have no world experience, never shot one, never held one.
I'm bit by the bug now and am looking at January to submit a Form 1 and build a suppressor for a .357 Rossi that I have.
Idea is to slow down the escaping gas... so after looking online at many, many designs of monocores, baffle designs I've come up with something similar to one that I've seen online that a person made.
The idea for me on this is that i'm not a skilled lathe operator, but could make baffles as I have the ability to do whatever I put effort into..
The image is just the monocore. It would be drilled with the same pattern at 90 degrees, so think of it like drilling two sides of a rectangular piece of steel.
I would make it from stainless steel, between each hole there would be a minimum of say .1-.2" of material on outer edge. Excuse the drawing, I could make a better one on the computer if I spent more than a couple minutes on it.
Idea would be to start with a large cavity that's 80% of the width of the core. Then I would step it down to 75% for the next holes until I started to walk towards the end of the core and at that point I would probably have a 50% hole. if I used 1.5" diameter stock, 50% would be a 3/4" hole, 75%=1-1/8" etc..
From what I gather when a form 1 is submitted you specify length, and caliber, without needing to give specific details about baffles etc. So if this design flopped I would have an outer that I could manufacture a new inner correct?
Excuse the dimensions, they aren't exact nor is everything next to each other like I wanted.
for clarification:
Be gentle, correct me easily... Thanks in advance.
I'm bit by the bug now and am looking at January to submit a Form 1 and build a suppressor for a .357 Rossi that I have.
Idea is to slow down the escaping gas... so after looking online at many, many designs of monocores, baffle designs I've come up with something similar to one that I've seen online that a person made.
The idea for me on this is that i'm not a skilled lathe operator, but could make baffles as I have the ability to do whatever I put effort into..
The image is just the monocore. It would be drilled with the same pattern at 90 degrees, so think of it like drilling two sides of a rectangular piece of steel.
I would make it from stainless steel, between each hole there would be a minimum of say .1-.2" of material on outer edge. Excuse the drawing, I could make a better one on the computer if I spent more than a couple minutes on it.
Idea would be to start with a large cavity that's 80% of the width of the core. Then I would step it down to 75% for the next holes until I started to walk towards the end of the core and at that point I would probably have a 50% hole. if I used 1.5" diameter stock, 50% would be a 3/4" hole, 75%=1-1/8" etc..
From what I gather when a form 1 is submitted you specify length, and caliber, without needing to give specific details about baffles etc. So if this design flopped I would have an outer that I could manufacture a new inner correct?
Excuse the dimensions, they aren't exact nor is everything next to each other like I wanted.
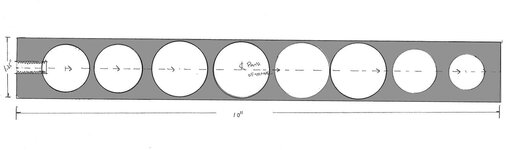
for clarification:
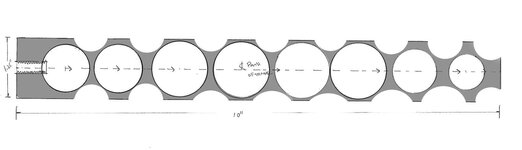
Be gentle, correct me easily... Thanks in advance.