Bronze Supporter
- Messages
- 5,296
- Reactions
- 4,917
Let me start by saying that I am completely ignorant of all things welding.
I used a stick welder like 10yrs ago to weld a bracket to a piece of sheet metal... it looked like hell, but it worked.
And thats pretty much it.
Now I am looking at taking on another small project.
I have a travel trailer that I need to install a lift kit (spring over axle) on and it *suggests* that the new perches be tack welded to the axle... Seems cheesy to me despite the positive reviews the kit gets...
https://www.amazon.com/gp/product/B008OADK9G/ref=ask_ql_qh_dp_hza
Anyhow, I am thinking that I will install this and weld the entire length of the bracket just to be safe.
I just happened to have a Lincoln gasless wirefeed welder which uses .030 wire
is this going to be adequate for the job? I believe that the brackets are 1/4" thick.
I went out and made some practice runs... here is a piece of 3/8" AR500 and the bolt is 9/16" zinc plated
I welded both sides along the whole length, about 8", and it held... slammed it around on the concrete a few times and it held
This is without any prep work at all, just clamped the bolt down and went at it.
Again, not sure what Im doing with this... can you critique me on this or give a couple of pointers?
I used a stick welder like 10yrs ago to weld a bracket to a piece of sheet metal... it looked like hell, but it worked.
And thats pretty much it.
Now I am looking at taking on another small project.
I have a travel trailer that I need to install a lift kit (spring over axle) on and it *suggests* that the new perches be tack welded to the axle... Seems cheesy to me despite the positive reviews the kit gets...
https://www.amazon.com/gp/product/B008OADK9G/ref=ask_ql_qh_dp_hza
Anyhow, I am thinking that I will install this and weld the entire length of the bracket just to be safe.
I just happened to have a Lincoln gasless wirefeed welder which uses .030 wire
is this going to be adequate for the job? I believe that the brackets are 1/4" thick.
I went out and made some practice runs... here is a piece of 3/8" AR500 and the bolt is 9/16" zinc plated
I welded both sides along the whole length, about 8", and it held... slammed it around on the concrete a few times and it held
This is without any prep work at all, just clamped the bolt down and went at it.
Again, not sure what Im doing with this... can you critique me on this or give a couple of pointers?
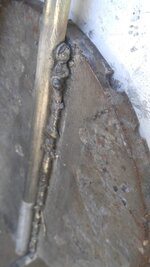