- Messages
- 6,824
- Reactions
- 17,613
Earlier this summer I became interested in reloading buckshot shotshells for my 20 gauge because they had become unobtanium. I had a lot of fun figuring that out ( Shotshell Loading Without A Press ) but then all the buckshot dried up and so I started thinking about getting a mold, but then the #1 buck molds disappeared, and so I decided to try to make a mold. A lot of this stuff is coming back in stock but that's no reason to abandon a project once started.
I wanted to use my Lee handles but in the end I couldn't get the set screw out so for this test I just used channel locks to hold the mold together while pouring. Not ideal but I'll order some bare handles. Anyway, I started with aluminum bars and cut out some channels to match the lee molds:
Then flipped the bar over and carved the mold faces (the one on the left is after the finishing pass, the one on the right is getting a finishing pass after roughing -- I messed this set up though and had to redo farther down the bar):
This was the end product. I decided to try carving centering pins and also inserting steel pins -- carving the pins was not great because you can see my face isn't super smooth and with the pins in the way, I can't sand the face. It also takes ages to carve away all the metal around it -- about 20 hrs on my machine. I won't do that again -- I'll use the steel insert pins:
I also didn't have my CNC router cut the pieces out -- I used a sawzall to separate them because again, with a machine like mine that would take ages and I just wanted to see if it would work, so wasn't going for pretty. This is the end result -- you can see the side that does not have carved pins looks nice after sanding on a flat surface. The carved pins make that impossible:
I didn't keep full strings of non-reject shot, but here a few strings of rejects:
Close up of shot I accepted. These aren't perfect at all. The mold depth was a little shallow so they are somewhat flattened (I need a smaller diameter ball mill -- I think the machine won't go to the full depth because the smallest diameter ball mill I have is 1.5 mm -- I should get 0.5 or 0.25 mm and see what happens). The two mold halves also don't center absolutely perfectly and of course there is roughness where I cut the sprues. I tried tumbling and vibrating but I don't have an effective method yet. Also, I was aiming for #1 Buck and also trying to account for shrinkage -- I was a bit off. I've been loading shotshells with 12 #1 Buck pellets -- that would be too heavy with my home-made shot, so I went with 11 pellets (about 440 grains)
Despite the shortcomings of the finished shot, I decided to see how they did. My first test with the cylinder choke was about 1200 FPS and the IM just a little faster, but I was so excited I forgot to record the actual readings. Anyway, the result:
15 yards
Yellow marked holes with Cylinder choke -- about a 15" group.
Green marked holes with IM choke - a little less than 8" group.
So in the end, my imperfect shot did OK and I'm going to take a crack at a second version.
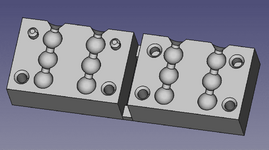
I wanted to use my Lee handles but in the end I couldn't get the set screw out so for this test I just used channel locks to hold the mold together while pouring. Not ideal but I'll order some bare handles. Anyway, I started with aluminum bars and cut out some channels to match the lee molds:
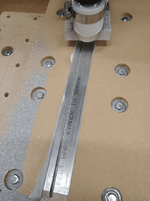
Then flipped the bar over and carved the mold faces (the one on the left is after the finishing pass, the one on the right is getting a finishing pass after roughing -- I messed this set up though and had to redo farther down the bar):
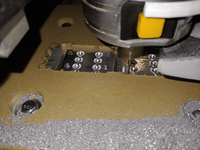
This was the end product. I decided to try carving centering pins and also inserting steel pins -- carving the pins was not great because you can see my face isn't super smooth and with the pins in the way, I can't sand the face. It also takes ages to carve away all the metal around it -- about 20 hrs on my machine. I won't do that again -- I'll use the steel insert pins:
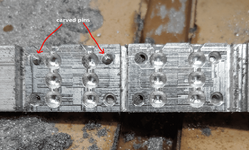
I also didn't have my CNC router cut the pieces out -- I used a sawzall to separate them because again, with a machine like mine that would take ages and I just wanted to see if it would work, so wasn't going for pretty. This is the end result -- you can see the side that does not have carved pins looks nice after sanding on a flat surface. The carved pins make that impossible:
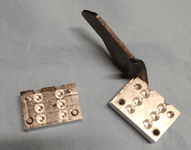
I didn't keep full strings of non-reject shot, but here a few strings of rejects:
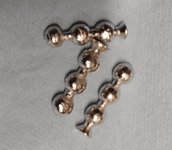
Close up of shot I accepted. These aren't perfect at all. The mold depth was a little shallow so they are somewhat flattened (I need a smaller diameter ball mill -- I think the machine won't go to the full depth because the smallest diameter ball mill I have is 1.5 mm -- I should get 0.5 or 0.25 mm and see what happens). The two mold halves also don't center absolutely perfectly and of course there is roughness where I cut the sprues. I tried tumbling and vibrating but I don't have an effective method yet. Also, I was aiming for #1 Buck and also trying to account for shrinkage -- I was a bit off. I've been loading shotshells with 12 #1 Buck pellets -- that would be too heavy with my home-made shot, so I went with 11 pellets (about 440 grains)
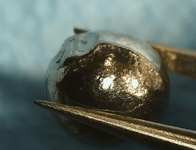
Despite the shortcomings of the finished shot, I decided to see how they did. My first test with the cylinder choke was about 1200 FPS and the IM just a little faster, but I was so excited I forgot to record the actual readings. Anyway, the result:
15 yards
Yellow marked holes with Cylinder choke -- about a 15" group.
Green marked holes with IM choke - a little less than 8" group.
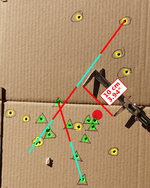
So in the end, my imperfect shot did OK and I'm going to take a crack at a second version.
Last Edited: