Bronze Lifetime
- Messages
- 11,325
- Reactions
- 25,956
Loaded 200 9mm rounds this morning. Had a half hour before a conference call, so thought I'd set it up for 223.
I always run a case through many times making sure the dies are all still zeroed.
VERY FIRST CASE gets stuck in the resizing die. Push the handle to get the ram back down and SNAP! Part number 29 snaps off at the shoulder.
Called Hornady customer service, no wait for an answer. Brad is sending a part. Awesome!
I always run a case through many times making sure the dies are all still zeroed.
VERY FIRST CASE gets stuck in the resizing die. Push the handle to get the ram back down and SNAP! Part number 29 snaps off at the shoulder.
Called Hornady customer service, no wait for an answer. Brad is sending a part. Awesome!
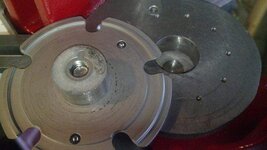
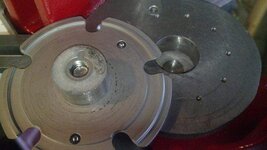