Gold Supporter
- Messages
- 24,691
- Reactions
- 37,485
I would like to remove just a bit of the rim thickness on the inside surface of some 444 Marlin cases. Any thoughts on an easy way to do that with out damaging the sidewall of the case? I might have a 100 or more to do this to.
The area where the pen is pointing to is the area I want to remove the material from.
The area where the pen is pointing to is the area I want to remove the material from.
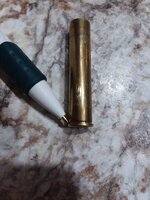